COST IRON
GRAY COST IRON
DUCTILE IRON
GRAY COST IRON
Gray Cast iron is an alloy based on Carbone & Iron. Has 3-3.5 % Carbone, although it has another chemical elements added during casting and before final freezing.
Except in special cases, cast iron where it is melted in a blast furnace called “Coupling furnace”, is mainly produced in electric induction furnaces. After melting completion, molten iron is poured into a holding furnace or mold. we are using electrical furnace in Navin Sanat Company.
The Gray Cast Iron is the most malleable ferrous which can make an involved or very thin shapes with. If the chemical composition of cast iron in the gray cast iron range and stage of cooling are properly and correctly, the carbon in the iron is isolated and makes graphite strips.
This type of cast iron has very good turning within its hardness. Its color is gray for that called Gray Cast Iron.
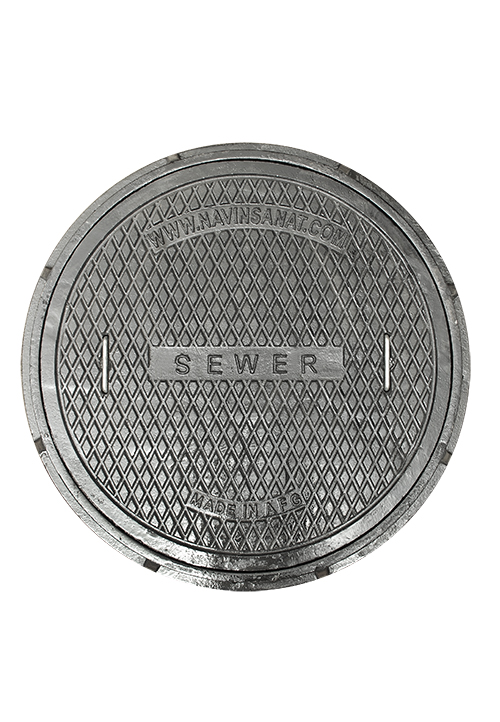
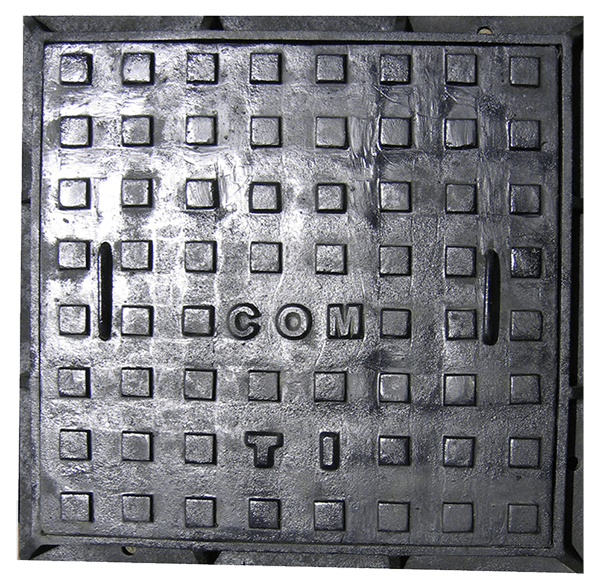
DUCTILE IRON
Ductile cast iron or malleable cast iron has ferity- puerility base, or both of them with ball shape graphite. Malleable cast iron in cooling down duration, its Carbon frizzed in ball or roundly shape.
In case ductile cast iron is useable to produce different parts of car engines, where it is more resistant than aluminum but steel is not necessary to use. Other important industrial usages including transportation diesel trucks, class 8 trucks, farm tractors, oil well pumps, etc.
It’s used from ductile cast iron for fabricating a large range of products such as manhole and handhole covers for water and sewer, staging clamps, accessories for industrial machines, car engines &, etc.
Ductile cast iron characteristics: low melting point, suitable casting, good shape making, well abrasion resistance & suitable malleability
Cost Irons Are Suitable for
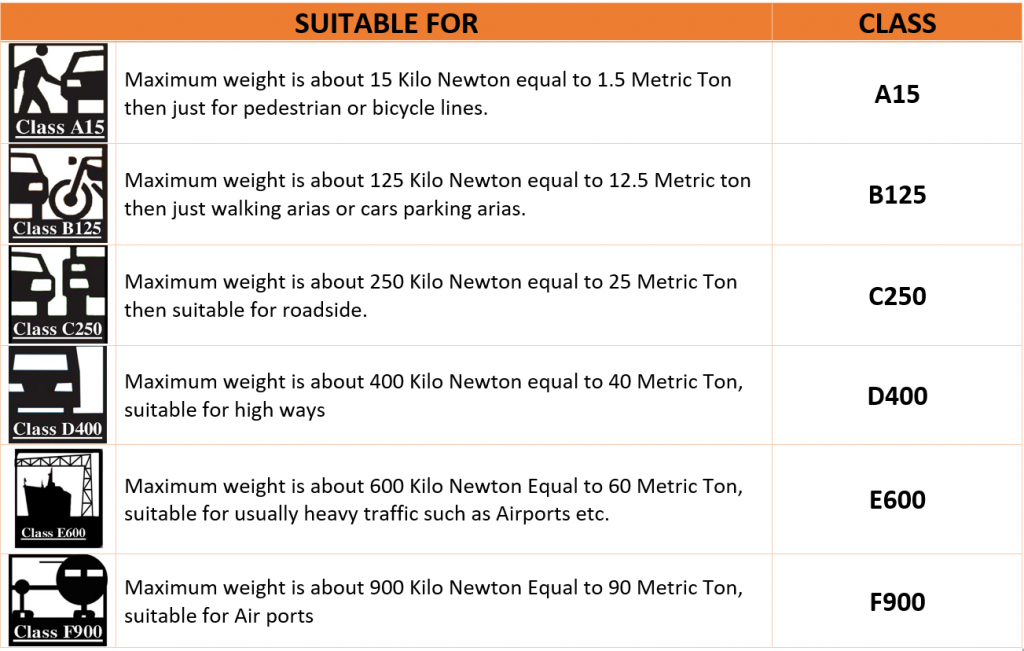
Cost Iron Process Step
Making flask mold casting metals
The first stage for casting cast iron is Model designing according to the order of customers.
The next stage is creating the main mold using the CNC machine. This mold actually is the ordered sample.
Then main mold called flask mold creates based on the samples. Flask mold is a kind of metal mold which sample being inside on.
Flask mold actually is a square metal frame which rounded the sample. Flask mold can be made in two method, one by aluminum, tow by steel or welded iron. After that, placed the sample inside the flask mold to starting molding by sand.
Molding by Casting sand
Inside of flask mold, the Co2 sand is poured to cover the entire mold. The silicon sand is poured after Co2 sand, the Co2 sand layer most not much thick to remove easily and cheaper.
The next step is sand is pressed by hammer to make compacted sand. After hand compaction Co2 gas is injected for sand more hardness. In sand method some perforation created in sand and gas in injected from that, after gas injection the mold closed and fastened.
Unpacking Casting Mold
After frizzing the molted in mold, now this is to split the mold. there are different steps for separate flask mold from the main mold.
We can do it with a vibrator also manually. Manually With pressing the main mold is separated from the flask mold and in the mechanical method, within the vibrating machine, the main mold separates from the flask mold.
Finalizing the casting
After all separation the casting piece from the sand mold, cleaning and equalizing the piece step with Shotblast Machine.